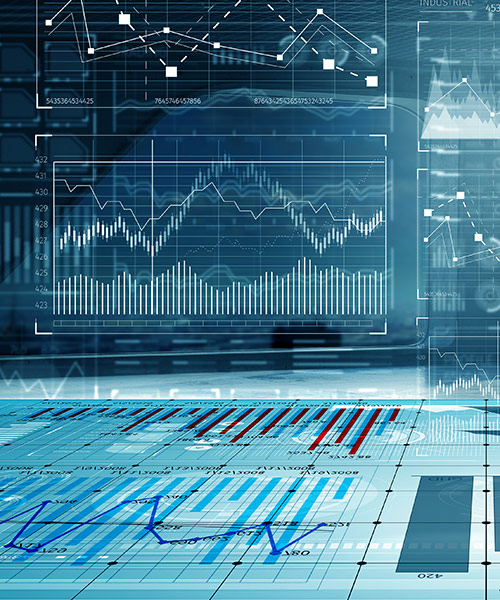
These algorithms now accommodate both in-service disbonds and other defects, as well as the reduced datasets found in MAUS generated UT C-scans. The output of our algorithms can be mapped to 3D CAD models along with other digital data – creating a “digital twin” – to allow depth visualization of indications, identification and sizing anomalies in 3D, comparing data across multiple datasets to identify the growth of disbonds and other defects, and to map and track repairs/replacements to models. Taking into account flight hours, number of flights, and flight profiles will help predict appropriately timed maintenance cycles of the aircraft. The resulting “digital twin” will provide a better holistic view of the structure to improve the overall sustainment of the aircraft.