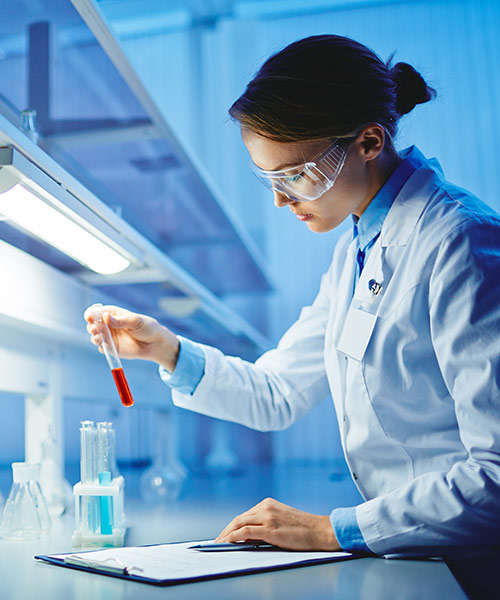
Commercially available gap-fillers are initially effective, but performance degrades under thermal and mechanical fatigue resulting in micro- and macrocracks within the matrix. A 50-fold increase in fatigue crack resistance at 73oF was obtained with the materials developed compared to the commercial gap-fillers tested. The same gap-filler material tested a -65 degrees F showed improvement of 75 percent in crack resistance.
The combination of mechanical and thermal fatigue generates the most aggressive stresses for gap-fillers on aircraft, where temperatures within the range of -65 degrees F to 250 degrees F are experienced. These stresses occur because of differential thermal expansion and modulus changes in the gap-filler material. Additional testing was conducted to replicate these stresses in the laboratory to determine durability over a range of temperature-stress profiles. The elastomeric gap-filler matrix was further refined and tested for qualification.