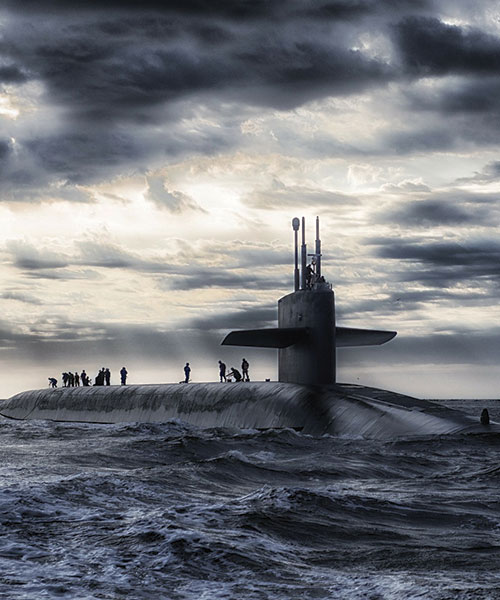
BondCoat™ is technology for making underwater connectors resistant to cathodic delamination. The Portsmouth connector is the most commonly used underwater connector on ballistic missile submarines (SSBNs). Due to electrical connector failures, submarines have required dry-docking as often as every two years.
TRI Austin performed shipboard inspections and laboratory connector failure analyses to identify possible failure mechanisms, and used accelerated life testing (ALT) and development of design modifications. Cathodic delamination of the rubber to metal bond in the connector can occur when the electrical field used in cathodic hull protection systems induces hydroxide ion formation at the bond interface.
TRI Austin developed and commercialized a solution to this problem that involves a nonconductive coating (NCC) formed from a plasma spray ceramic and polymer sealer. TRI’s Bond-Coat™ is now a fleet required standard for submarine MIL-C-24231 and MIL-C-24217 connectors. It is also used in down-hole connectors, offshore applications, and in other harsh environments that challenge rubber to metal bonds.
In test after test, Bond-Coat™ NCC outperforms standard overmolding preparations designed to protect hardware exposed to harsh environmental conditions. The result is a bond that can survive the most corrosive conditions and last five times longer.
Developed by TRI Austin for the U.S. Navy to fight cathodic delamination (pre-mature bond failure) of submarine connectors, Bond-Coat™ NCC’s metal pretreatment system is ideal for use in harsh environments such as industrial, sub-sea and down-hole operations. That’s because Bond-Coat™ NCC firmly adheres even rubbers and metals needed to survive chemical exposure and high-pressure, extreme-temperature conditions.